MATERIALI E PROCESSI MODERNI E FUTURI NEL SEA KAYAK
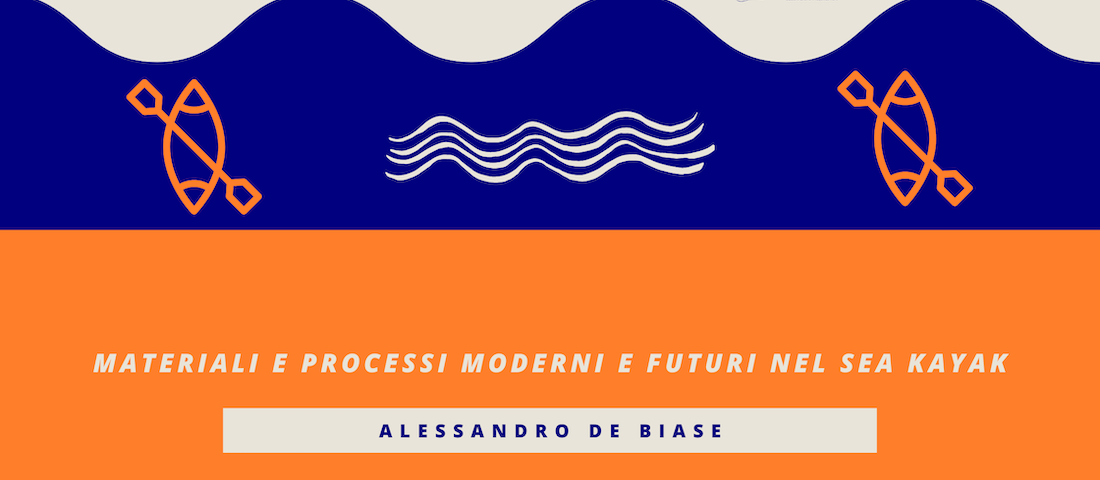
Negli ultimi 20 anni, i kayak e le pagaie da mare hanno beneficiato di significative evoluzioni, sia nelle geometrie, sia nell'utilizzo di materiali prestazionali e relativi processi di produzione.
Questo per renderli più sicuri, scorrevoli, leggeri, resistenti e riproducibili in serie, con costanti caratteristiche.


Quali sono le più recenti innovazioni e i possibili futuri scenari produttivi nel sea kayak?
a. Materiali
- I Materiali Compositi Fibrorinforzati rappresentano i materiali più prestazionali: sono caratterizzati dalla combinazione di fibre di rinforzo, inorganiche o organiche, tessute in particolari direzioni e impregnate in una matrice resinosa. Tra questi i più noti sono:
a. Tessuti compositi con fibre di Carbonio e Kevlar che garantiscono eccellenti proprietà meccaniche tra cui rigidità, resistenza all’impatto (non il carbonio con corpi appuntiti), leggerezza, estetica hi-tech, ma non sempre una facile lavorabilità e costi elevati.
b. Tessuti compositi con fibra di vetro: la Vetroresina tipo S, più rigida e resistente rispetto alla comune di tipo E, ne mantiene la lavorabilità, con migliorato rapporto costi / benefici
c. Tessuti con fibre di poliestere e vetro, il Diolene, per chi cerca maggiore resilienza rispetto alla vetroresina ma la facile riparabilità, rispetto al kevlar.
d. Dal 2010, sono una novità i Tessuti Compositi con fibra di Lino, più facili da smaltire a fine ciclo vita, rispetto a quelli che utilizzano fibre polimeriche, in quanto naturali.
Applicati a kayak e pagaie, i tessuti in fibra di lino offrono diversi vantaggi, tra cui resistenza agli urti, rigidità ma con ottima dissipazione delle vibrazioni causate da impatti sulle onde, leggerezza ed estetica naturale che si avvicina a quella del legno, con possibilità di colorazioni in base al sistema RAL. I compositi in fibra di lino si posizionano tra la vetroresina e il carbon-kevlar, quanto a proprietà meccaniche, leggerezza e costo. L’impiego non è ancora diffuso tra i grandi costruttori.
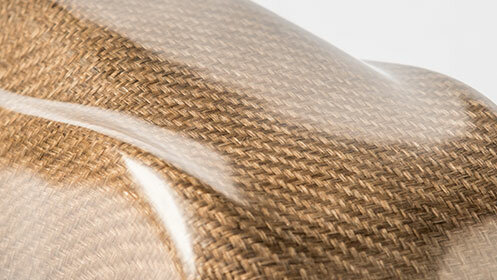
Fibra di lino
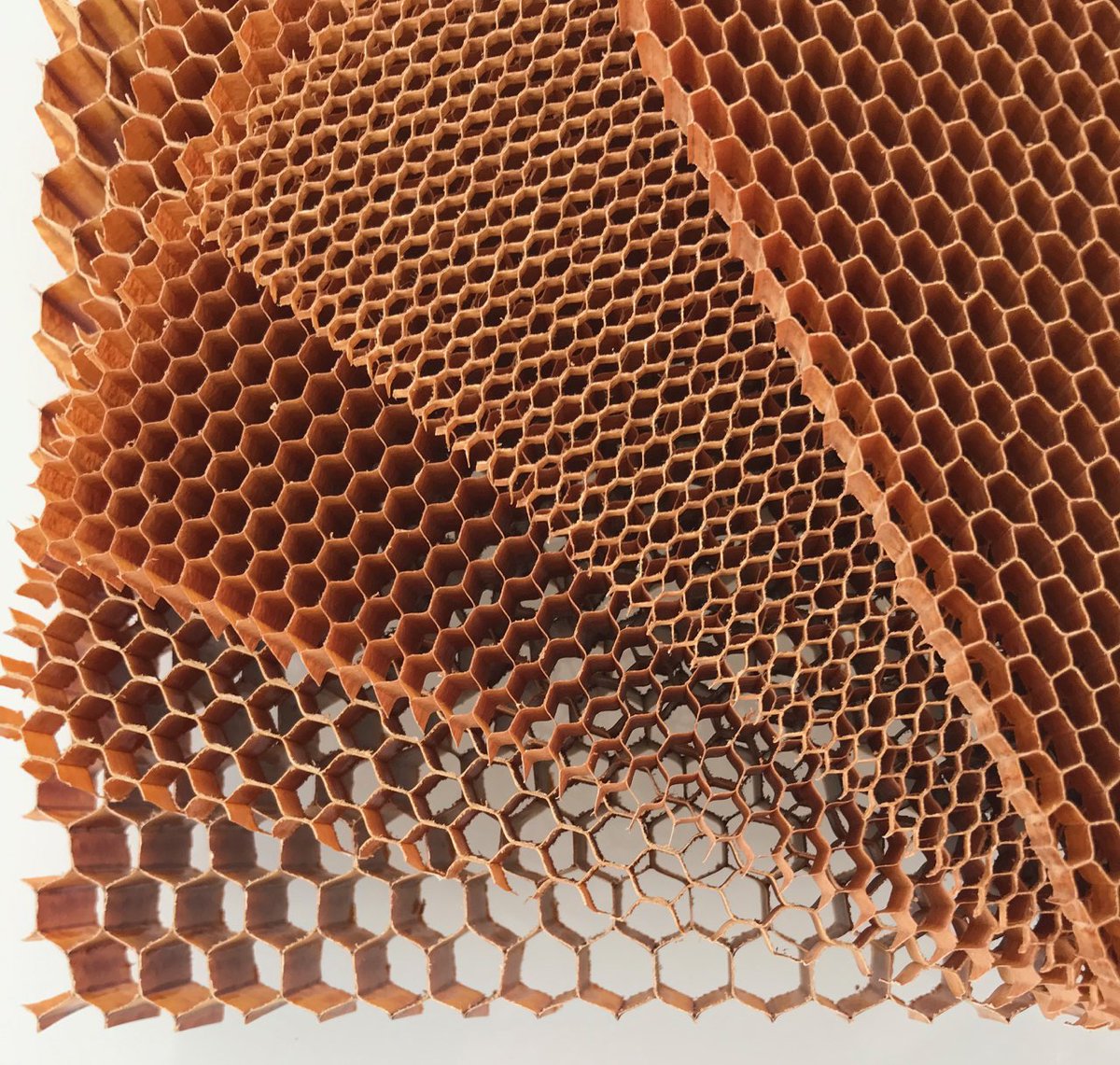
Honeycomb
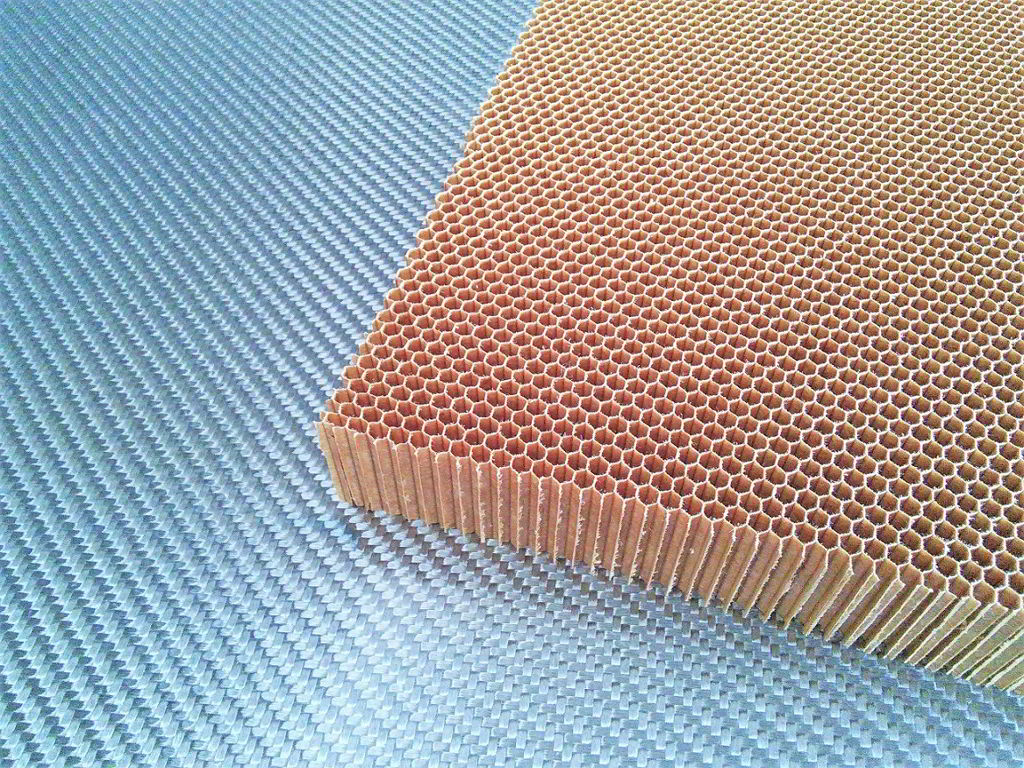
Nomex aramid honeycomb
2. l’Honeycomb è un materiale avanzato che impiegato nella costruzione dei kayak li rende molto leggeri e performanti: si tratta di una struttura alveolare, cava per il 90% del suo volume, resistente, realizzata in speciale carta aramidica impregnata con resina fenolica, attorno al quale poi si stratificano tessuti di carbonio, kevlar, fibra di vetro e gelcoat.
3. Le Resine poliesteri ed epossidiche tengono insieme le fibre dei materiali compositi. Novità in questo campo sono le Resine epossidiche con contenuto bio fino al 75%.
Resine con Grafene migliorerebbero l'adesione delle fibre nella matrice, con aumentate rigidità e resistenza alla fessurazione.
4. L’ABS è un materiale plastico interessante perché, in fogli, può essere termoformato per produrre kayak leggeri, quasi quanto quelli in composito, ma meno prestazionali, durevoli e facilmente riparabili. L’impiego non molto diffuso.
5. Il Polieteilene è il polimero ideale per produrre imbarcazioni per un uso reiterato anche su fondali duri e rocce. Il PE viene fuso, reso gelatinoso e fatto fluire in stampi rotazionali che plasmano kayak che risultano robusti ma un po’pesanti, che si deformano se esposti ad elevato calore e non facilmente riparabili. Oggigiorno, rispetto allo stampaggio con 1 solo strato, sono proposte a soluzioni sandwich multistrato per kayak in PE ad altà densità, più leggeri e resilienti.
b. Processi
1.I kayak fabbricati utilizzando tessuti compositi in fibra sono prodotti utilizzando stampi in vetroresina, in cui vengono lavorati con cura i tessuti impregnati con resine.
I processi Vacum-bagging e Vacum Infusion producono kayak ancor più leggeri e resistenti, implicando minimi scarti di resina e maggiore sicurezza per l’operatore, rispetto all’ impregnazione manuale dei tessuti con rulli (hand lay-up).
Con le tecniche di infusione sottovuoto, si combinano la sottrazione di aria dal tessuto ed un’accurata e controllata introduzione della resina con pompe speciali.
2. Tra gli scenari produttivi futuri nel sea kayaking potrebbe rientrare la Stampa 3D che consente la realizzazione di oggetti tridimensionali, mediante produzione additiva.
Questo processo, sempre più spesso usato anche in nautica da diporto, potrebbe consentire di stampare kayak con misure e geometrie personalizzate, in circa 10 ore.
Una volta inseriti i parametri (disegno, misure) la stampante 3D produce l'oggetto, strato dopo strato. Il Robotic Additive Manufacturing consente ad un ugello posto su un braccio meccanico robotizzato, di depositare polimero fuso, strato dopo strato, per creare la geometria progettata. Questa stampante robotizzata è molto evoluta perché i polimeri si caricano direttamente nel serbatoio dell’attrezzatura e non si impiega, come nelle altri stampanti 3D, un filamento che va sciolto per poi essere depositato.
Con il suo braccio meccanico, il robot raggiunge un raggio di oltre 4 metri in piano e altezza che consente di stampare scafi di oltre 5 metri di lunghezza.
Puo’ stampare innumerevoli matrici polimeriche, anche a base naturale, con diverse densità nella struttura del kayak.
Applicazioni potrebbero includere kayak personalizzati da gara e anche per paracanoa o per veri maniaci della prestazione.
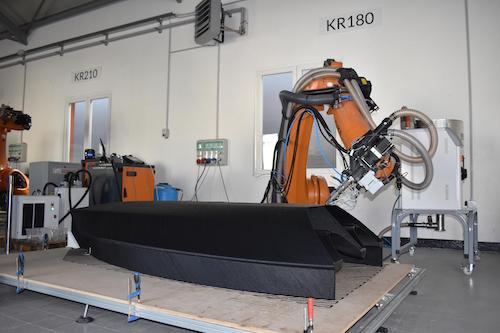
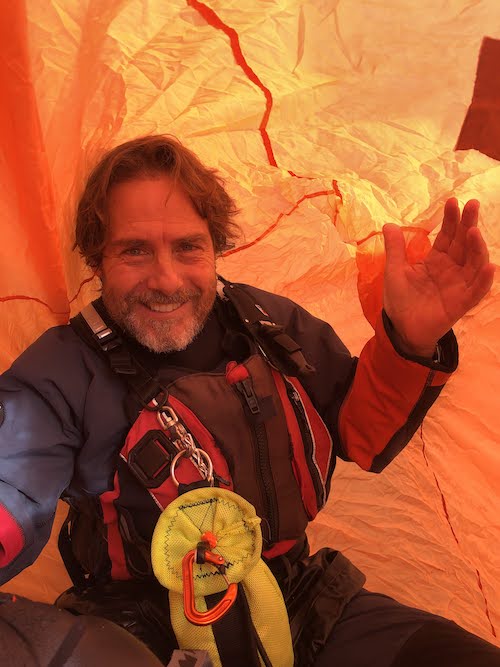
Articolo scritto da Alessandro De Biase
Sea kayaker da 7 anni e amante di escursionismo, in spedizioni di più giorni, ho circumnavigato l’Isola d’Elba, il Giglio, Ponza e Palmarola, S. Antioco e l’Isola di San Pietro e lungo le coste Sud della Corsica, della Sardegna e dell’Argentario.
Navigo costantemente sui Laghi di Como, Garda e Maggiore, mentre in mare, amo pagaiare in condizioni dinamiche e surf nel Levante Ligure ed in Veneto.